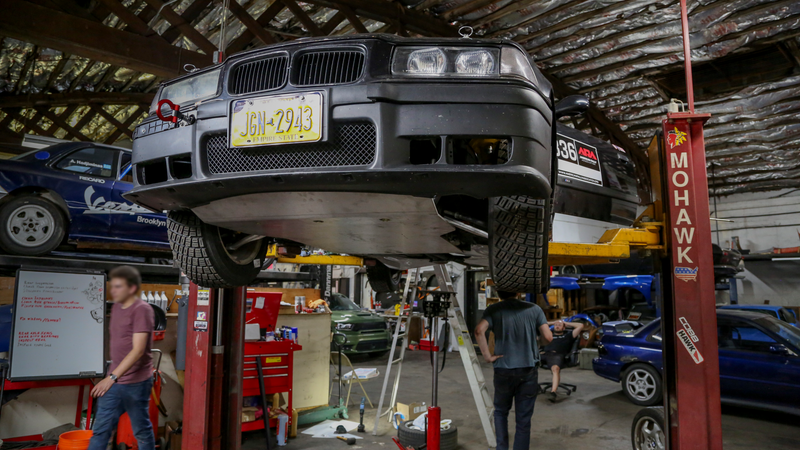
I thought mounting underbody protection to my BMW M3 rally car would be mostly quick and easy. Well, that was a dumb thought!
To run a rally is to intentionally beat the hell out of your car. You run on rough roads, with ruts and jumps to bottom out on, and you run on gravel roads. Every time you’re sideways, you’re pelting the underside of your car with rocks. As such, you need to have underbody protection, and this is both advised and mandated.
It’s both for the safety of your car (you don’t want to puncture your low-hanging oil pan) and for the safety of everyone else in the forest. (You really don’t want to puncture your fuel tank and send flames trailing off into the dry woods.)
I left the skid plate and fuel system covering as one of the last to-do items on my rally car before its debut at New England Forest Rally on Friday. I figured, “Oh, I’ll just go buy an out-of-service stop sign and bolt it up to the bottom of my car!”
Advertisement
Haha, not quite, naive Aaron from two weeks ago.
Aside from stop sign metal probably not being thick enough or strong enough for the rocks I might (will?) be coming in contact with, the E36 also pretty much has nowhere to bolt a skid plate to. Before we removed it, my front sway bar was the lowest point on my car. This meant a whole set of mounting bars had to be fabricated for the car.
Advertisement
Also, the skid plate metal would need some sort of bend at the front of it. Even if the car were perfectly set up underbody protection, I would probably still need to bring the plate to a metal shop with a brake so that it could be bent properly.
Since I can barely wrench and definitely can’t fabricate or weld, I brought the car over to Bill Petrow at Broken Motorsports in New Jersey, a place far more capable of building skid plates than I’ll ever be. Broken is a big name in the Northeast rally scene, and it’s sometimes hard to find a car running in an event that hasn’t had some some work done to it (if not built entirely) by Petrow and crew.
Advertisement
Petrow used three bars to fit my new massive skid plate to the car. Two of the bars were mounted toward the front of the car’s frame rails, with one as a primary mount and another angled as a support bar for when I inevitably become too friendly with some Maine rocks. The other bar was mounted further back on the frame rails.
Advertisement
Of course, those bars had to be measured, bent properly, mounting plates had to be welded to the frame and insert nuts also had to be welded to the bars so that the skid plate could actually be bolted up. And the whole thing had to get painted!
This shit took a hell of a lot of time.
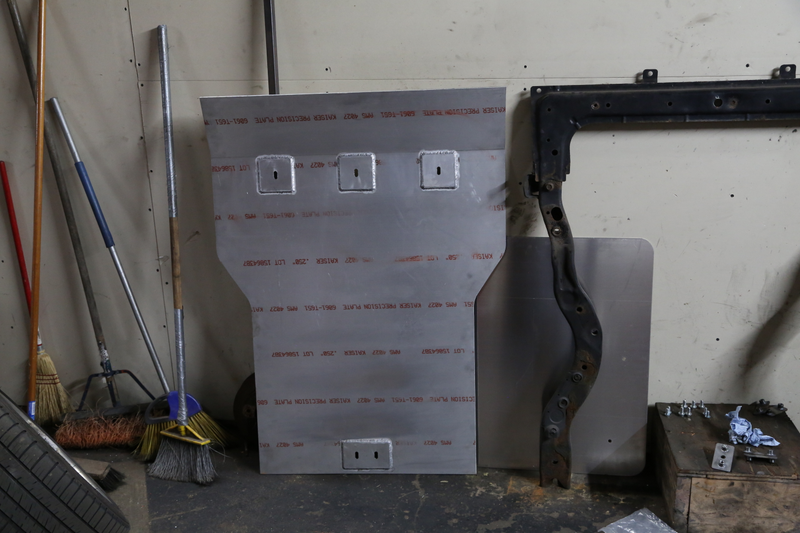
Advertisement
Thankfully, Petrow had a large, pre-bent and pre-cut slab of quarter-inch-thick 6061-t6 aluminum that was made for a Subaru Impreza, which managed to fit pretty nicely on my car.
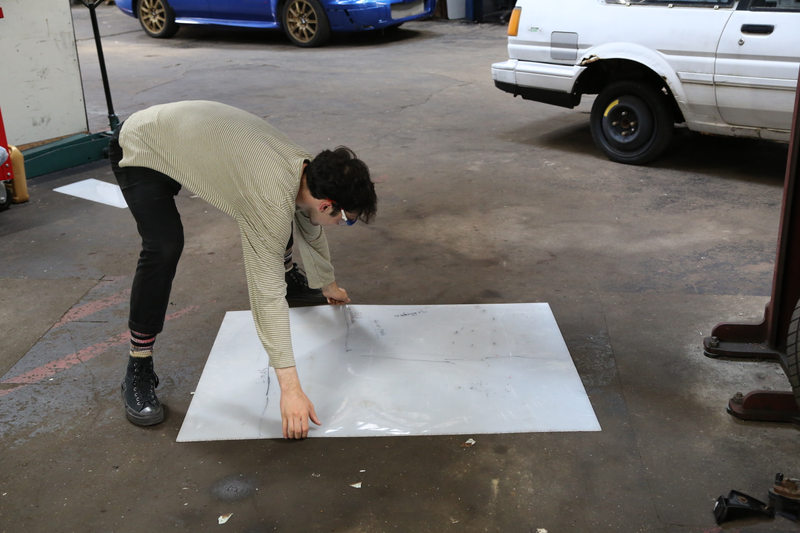
Advertisement
While he worked on protection for the front, myself and my friend Emmet grabbed some high-density polyethylene plastic to cover up the fuel tank, fuel lines, and brake lines in the rear of the car. This wasn’t too complicated; we held the plastic up to the underbody of the car and to the areas we’d need to cover, and outlined them with a sharpie. Then we cut it with a bandsaw and used rivet nuts to hold them in place under the car. For the fuel tank covers, we also zip-tied them to the rear lower control arms, so that they would be allowed some movement with the car’s suspension travel.

Advertisement
Not only is this kind of protection smart for off-road, gravel-trail racing like rally, it’s actually required for competition with the American Rally Association, NEFR’s sanctioning race organization. Cars have burned down at NEFR before, and this kind of protection is very much necessary not only to keep everyone competing safe, but also keep the somewhat-flammable forests of New Hampshire and Maine from getting too crispy this summer.
Between waiting for some hardware, doing all the measurements, fabricating everything, and actually mounting it up to the car, the whole process took about three workdays in the shop.
Advertisement
But I sure as hell am happy it got done. Let’s just hope none of this really has to be put to the test.
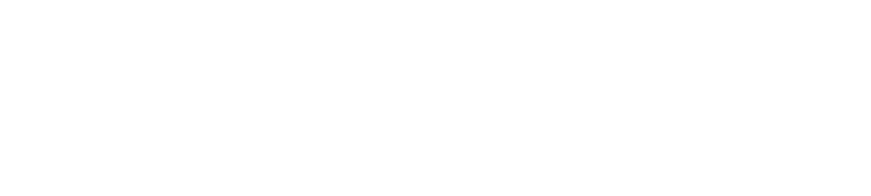