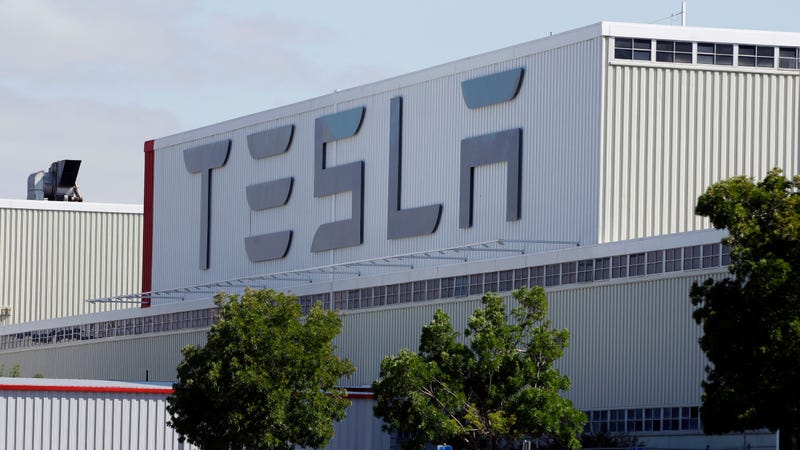
Remember way back in 2018 when one of the biggest stories in the automotive world was whether Tesla could meet its arbitrary self-imposed production targets by building a car factory in a tent in the parking lot of its existing car factory? They certainly did boost production, even if the much ballyhooed $35,000 Model 3 functionally doesn’t exist and reports of quality issues have cropped up here and there throughout.
Well, a new report from CNBC helps explain both how the company was able to boost production and what may be causing some of the quality issues. Electrical tape:
At the same time, workers were encouraged to take shortcuts to hit their production goals in the tent, according to five people who work or worked there recently.
For example, when it’s cold in the tent, workers tend to break a high number of plastic brackets and housings that hold critical electronics in place inside of the Model 3, according to four of these people.
Rather than waiting for replenishment teams to deliver boxes of new plastic parts to their stations in GA4, they said, supervisors told workers to use vinyl electrical tape to make quick fixes. Carlos Aranda says he personally visited Walmart multiple times to buy the tape and other items for production associates.
Missing bolts, nuts, or lugs:
Five people who work or worked in the tent in 2019 said they would frequently pass cars down the line that they knew were missing a few bolts, nuts or lugs, all in the name of saving time.
Advertisement
And reduced water testing:
Current and former employees also said Tesla reduced “water testing” on cars as the company began ramping up production of Model 3s.
In a water test, a vehicle goes into a booth where jets blast it with water from all different directions. Any leaks in the seals are immediately found and fixed. The tests take about 10 minutes each.
In late 2018, Tesla changed its policy and now only conducts sample testing for water leaks on Model 3s.
Advertisement
Tesla, of course, denies all of this. In a statement issued to both CNBC and Jalopnik, a Tesla spokesperson said “The anecdotes reported by CNBC from a few unnamed sources are misleading and do not reflect our manufacturing practices or what it’s like to work at Tesla.”
But Tesla’s claim that all the anecdotes come from unnamed sources is not correct. Two former employees, Carlos Aranda and his wife, Maggie, are on the record in the CNBC story. Six unnamed current and former Tesla employees confirmed their claims.
Advertisement
Tesla further told CNBC that Carlos Aranda was fired “for a Twitter post that went against its Workplace Violence Policy” but did not provide CNBC with any record of the tweet. It is, of course, deeply ironic that Tesla would claim to have fired anyone for a bad tweet.
In any event, as for the specific allegations of cut corners to meet production goals, a Tesla spokesperson touted the company’s robust quality assurance process. “In order to ensure the highest quality, we review every vehicle for even the smallest refinement before it leaves the factory. Dedicated inspection teams track every car throughout every shop in the assembly line, and every vehicle is then subjected to an additional quality control process towards the end of line.”
Advertisement
The company also told both CNBC and Jalopnik that the cables and brackets are supposed to have electrical tape on them; that’s how they receive the parts from suppliers.
But here’s what CNBC had to say about that:
Current and former GA4 workers acknowledged this, too. However, they made a distinction — the GA4 workers use tape to fix housings or brackets with cracks or to stop parts from vibrating in the car if they aren’t snapped or fastened in perfectly. That’s not the same as “factory tape,” they said.
Factory tape is high-quality and looks as if it’s shrink-wrapped on a part, always in the same place. Much of it is wound carefully around bundles of cables and wires in a perfect spiral. The tape that workers would apply in a Model 3 typically has hastily cut or torn ends and varies in placement.
Advertisement
All that being said, it’s noteworthy that at least one of the specific claims—about the Model 3 not being subjected to robust water testing—aligns with a very specific report of a Model 3 bumper falling off in the rain less than half an hour after driving off the lot, something that absolutely should not happen to any car at any price point.
Advertisement
These quality issues sound like the unintended consequences of aggressive production targets, and one of the reasons sophisticated management teams avoid pushing factories beyond reasonable capacity. Is it so farfetched that Musk’s “production hell” mentality, which taxed him personally mentally and physically, likely trickled down the management chain to the point where even assembly line employees felt pressure to prioritize quantity over quality?
Regardless, it will be interesting to see if the Model 3 experiences widespread reliability issues down the line as some of these cut corners come home to roost. If it does, expect wait times for Tesla repairs to become even longer.
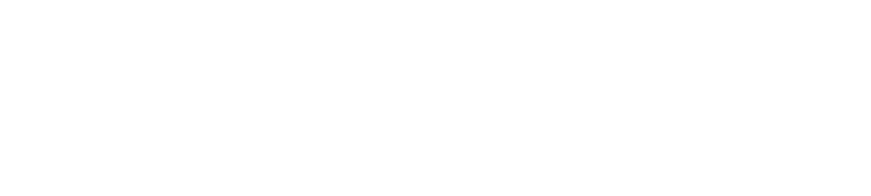