
Building a car from scratch in your basement is hard enough to make you a bit of a hero to the rest of us. Going off-plan to completely re-engineer the design of the car, adding a turbo and doing all your own carbon fiber work is the stuff of legends. Meet Jon Frecks, whose home-built Lotus Seven replica rules hard.
We all have a love-hate relationship with Haynes manuals, but would you build a whole car based off of one? Believe it or not, the same publisher that brought us the cryptic phrase “installation is the reverse of removal” has an entire book on how to build a Lotus Seven replica at home. Frecks used the book as a starting point, but found himself deviating from the book’s instructions by page two in order to make the best, lightest car he could.
“I’ve always wanted to build a car and Lotus has always been one of my favorite makes,” Frecks told us in an email interview. It’s only natural that he picked one of Lotus’ biggest, most enduring and most iconic hits:
The Seven.
Advertisement
Advertisement
A Fresh Take On A Legend
The Colin Chapman-designed Lotus Seven dates back to the late 1950s and has been around in various forms ever since, simply because it’s great at getting the job done. Pure Lotus all the way: simple, lightweight, fun.
Numerous kit companies, authors and wrenchers have given us their versions of the Seven race car thanks to its delightful, no-nonsense design. Caterham is among the most famous Seven makers in recent years, but versions are also produced by the likes of Birkin, Westfield, Superformance and even beloved oddball Mitsuoka.
Cars built on the plans in Chris Gibbs’ Build Your Own Sports Car are referred to as Haynes Roadsters, thanks to the book’s infamous publisher.
Fortunately, Haynes Roadsters also popular enough to have some parts support, as Frecks chose the Haynes Roadster design in part because he could simply order a nose cone and scuttle that fit the car and its 44-inch-wide cockpit instead of having to mold his own. He also liked that the design had an independent rear suspension.
Advertisement
Advertisement
Yet Frecks also works as a manufacturing engineer, so he likes the design and build process—so much so that he started researching ways to improve upon Gibbs’ plans early on.
“I started out with the
Locost USA forum. From there I built up a small library of books on chassis design, suspension dynamics, all of Carroll Smith’s books, and Keith Tanner’s How To Build a Cheap Sportscar,” Frecks told us.
What he discovered in his mounds of research was that there were still ways to simplify the design. Chapman would’ve been fine with that, I bet.
“Most of the [Seven replica] chassis designs are one-dimensional, meaning it’s a chassis that you bolt an engine and transmission in, slap on some suspension, and throw in some seats,” Frecks explained. “I’d like to think that my chassis emulates a race car chassis. I started with wheels and moved my way in. All of the load paths are tied together, everything is triangulated, everything is thought out.”
Frecks took the basic dimensions of the Haynes Roadster design and worked outwards from the main components of the car to completely rethink the chassis design.
Advertisement
Advertisement
“[The] seats, engine, transmission, and suspension interface points were located first, then the chassis was designed to connect those points with the least amount of material in the straightest direction,” Frecks elaborated.
With a rethought design in mind, Frecks’ dream car came together in his spare time over the course of a decade, with it finally getting licensed for road use in 2017.
“This was my build. If I didn’t want to work on it today……guess what, I didn’t,” Frecks said. “If I didn’t have enough funds, I could wait until I did, or more often than not I’d just figure out how to make the part myself.”
Advertisement
Advertisement
Putting It All Together
A 1990 Mazda Miata with over 180,000 miles was soon acquired for $800 to kick off the project. The engine ran, but the car didn’t drive, making it the perfect cheapo parts donor.
“I spent a year getting it road worthy enough so that I was confident enough that after I disassembled the whole thing and put it back together it would actually run,” Frecks told us.
Best of all, Frecks managed to make some money on his donor car in the end. “After I scavenged the pieces I needed (drivetrain, spindles, brakes, steering rack, gauges, etc.) I sold everything [I didn’t need] including the shell to recoup my money, and then some,” he said.
Advertisement
Advertisement
In 2009, Frecks started work on the chassis itself in his basement, cutting, notching and welding the necessary tubes together to make it all happen.
“It’s funny how people ignore the 1,000 technical problems it takes to solve when designing and building a car but ALWAYS ask, ‘How are you going to get it out of your basement?’” Frecks told us. Having a walk-out basement certainly helped, although many parts were shuttled in one piece at a time with the help of Frecks’ family as well as a Radio Flyer wagon.
The finished chassis had a 90-inch wheelbase and five inches of ground clearance, with a track width of 56.6 inches in the rear and 55.5 inches in the front. He had to heighten and lengthen the pre-made scuttle and nose cone to fit his design, but it seems worth it to be driving a car that is truly his own.
Advertisement
Advertisement
The independent rear suspension kept the donor Miata’s track width, and the front was Frecks’ own wishbone design. DR5885 Proma Star coilover shocks went on all four corners with 250-lb, 12-inch springs in the front and 275-lb, 12-inch springs in the rear, although even this was a matter of trial and error.
The rear had to be reworked after running into clearance issues between components with the shocks installed. He did incorporate room for the stock Miata sway bar, though, in case he wants to tinker with that in the future.
Next came the modification and installation of the 1990 Miata’s manual steering rack. To shorten the rack by seven inches to fit the new car, Mark sinply cut off the ends and re-tapped them to fit the inner tie rod ends’ threads. Fortunately, the tubing was just the right size for this to work.
The hardest part, however, was yet to come. The lightweight chassis was relatively easy to move around the basement using a home-built wooden stand to get just the right angle on the welds, but still needed all the components that make it a car: the engine, transmission and interior.
Advertisement
Advertisement
Complicating matters after the chassis had been mostly figured out was the addition of a BEGI Shanghai-S Turbo kit. Frecks had always liked the idea of turbocharging the Miata engine, but ultimately decided that it would be too difficult to add one after the fact. So, the turbo kit was acquired mid-build and proved to be Frecks’ hardest part to figure out due to the small confines of the car he’d started building.
“The problem was that I needed to know where the turbo was so that I could place the steering column, where the exhaust going to exit the chassis, and how [to] stiffen the engine bay with all the oil, water, exhaust, [and] intake fighting for the same real estate,” Frecks explained.
“The compromise I employed is [to] start with the turbo and all its plumbing and just run with the wastegate open. The Megasquirt PNP [engine management system], bigger fuel pump, injectors, [mass air flow sensor] delete are all waiting patiently in the basement until next year.”
Luckily, the turbo components cleared the steering rack, which was Frecks’ main concern. Fitting everything around it, however, still proved to be a giant time-suck.
Advertisement
Advertisement
“Progress really slows down when you get down to the nitty gritty detail fab portions,” Frecks explained on his Locost USA build thread. Even after the radiator was in, the seat and harness mounts were figured out, and the gas tank was complete, Frecks admitted that he changed the routing of the gas lines almost any time he touched the car for a while.
“For only having a little room to work in, I can sure find a lot of different paths to take,” he continued.
A pedal assembly from Southwest Speed went in the car along with a custom throttle pedal that Frecks designed to use with an unmodified stock Miata throttle cable. This proved to be tougher than Frecks really wanted it to be, as he admitted to us, “I think I designed and fabricated the throttle pedal three or four times.”
Advertisement
Advertisement
But he eventually figured it out, and moved on to installing other necessary things: a roll bar kit and windshield from Kinetic Speed, and all the wiring for the electrical systems of the car.
The only pieces Frecks really had to get help with from a shop were the driveshaft and a downpipe, which needed a TIG welder Frecks didn’t have at home. However, the driveshaft and downpipe were Frecks’ own designs, and Frecks even cut and tacked together the downpipe using his MIG welder at home before the shop finished out the welds for him.
“I’m pretty proud to say that I designed and built just about everything,” Frecks said.
Adding Lightness, But Definitely Not Simplicity
Then there was the matter of installing a body onto the car. Built-from-scratch Sevens like this are often called “Locosts,” but Frecks joked that he wasn’t going to cheap out and use simpler to install but heavier metal sheeting for the body of the car. Instead, he went for composites, as he had prior experience working with them and had the necessary materials around to do so.
Advertisement
Advertisement
“I did go overboard on the composites work, but that is something that I enjoy doing,” Frecks told Jalopnik. “Sure, a sheet of .050 aluminum is cheap and I could have skinned my floor and side panels in a day, but that’s what everyone else does. Not too many people utilize fiberglass, Kevlar, carbon, honeycomb core, pasticore, and corecell to make all of the panels. Sorry Colin, I didn’t simplify, but I did add lightness.”
Carbon fiber was used to finish off the dash, firewall and front fenders, and the rest of the body panels (including the firewall, transmission tunnel and even the load-bearing floor panels under the cockpit of the car) were finished out in various combinations of kevlar, carbon, fiberglass and core for a significant weight savings over aluminum sheeting. The finished hood, for example, weighed less than five pounds.
Advertisement
Advertisement
Additionally, it looks cool. Look, I fully admit that “carbon fiber everything” is my preference whenever possible. I would gladly even own and use a carbon fiber toilet if such a thing existed, for lightness! Or something. Just gaze in awe at all these pretty weaves on Jon’s car. This exactly the kind of delightful overkill that I love to see come out of people’s home basements.
“Don’t make me do the cost,” Frecks wrote of his composite work in his build thread. “It’s definitely more expensive—think double or triple the cost for raw materials alone.”
Advertisement
Advertisement
“Add in consumables like bagging material, peel ply, breather cloth, then the tooling, vacuum pump and finally my precious time and you quickly realize why pre-made composite sheet stock costs a small fortune,” he continued. “But this is my build, I like composites, and I already have the knowledge and tooling to make the parts.”
Worth it? Super worth it.
Advertisement
Advertisement
Once the body panels were ready, the chassis got painted black in a corner of Frecks’ garage, the body panels were sanded down and sprayed in white, carbon fiber pieces were clearcoated and it was assembly time. The engine was finally installed in the car with fresh seals, gaskets and paint in late 2016.
First start!
By mid-January 2017, it was already running. A few fittings weren’t tight enough and the air flow meter was installed backwards on the first start-up, but these items were soon fixed.
First drive!
A rear cover was installed using material from Composite Envisions/Elite Motoring, and soon, it was registered for road use. An inline marine bilge blower was also added to draw air from in front of the radiator over the exhaust and out the hood to keep the car cool when it’s not moving.
Advertisement
Advertisement
The real beauty of Frecks’ build is that many of the measurements, composite specs and other nitty gritty details are documented on his build thread on the Locost USA forums here. If you’ve ever wanted to know more about building a car from the ground up, gaze in awe at far more fabrication photos than we have the room to fit on here, or simply want to follow along with the car’s future adventures, check it out.
Advertisement
Advertisement
Advertisement
Advertisement
We’re featuring the coolest project cars from across the internet on Build of the Week. What insane build have you been wrenching on lately? Seen any good build threads we should know about? Drop me a line at stef dot schrader at jalopnik dot com with “Build of the Week” somewhere in the subject line if you’d like to be featured here.
[H/T Chris!]
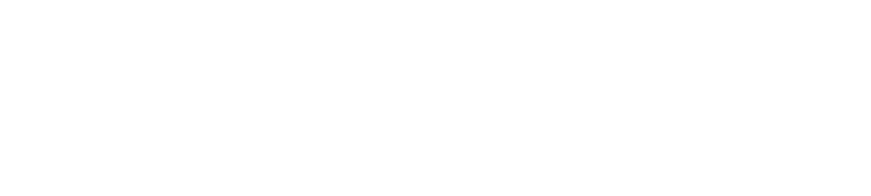