
I somehow managed to get my 250,000 mile Chrysler Voyager diesel through Germany’s rigorous TÜV inspection, but that didn’t mean the van was ready for a long European road trip. I still had a serpentine belt to swap, and I wanted to install a new water pump just to be safe. This should have been easy, but instead, it was by far the most difficult job to date.
Take a look at the photo above, which shows the back side of my engine as viewed from behind, just above the front suspension subframe. If it’s not obvious what the problem is, allow me to explain: The pulley is stuck on the water pump due to two Allen bolts that I—in my infinite wisdom—stripped. With the pulley in place, trying to remove the pump resulted in the pulley hitting the van’s unibody rail (a part of the body) before the impeller could clear the pump shroud/housing. In other words, because of the irremovable pulley, the pump was essentially stuck between the motor and the body.
To solve this, I had to remove the shroud, which was held to the back of the engine block via four studs. In addition, I had to undo the three Allen bolts holding a coolant pipe to the back of the shroud, plus there was a small hose going directly into the shroud, so I had to remove a hose clamp.
This all sounds easy, except access was horrible.

The two nuts on the lower studs holding the shroud to the block were no problem. They were off in a matter of seconds. The upper nuts, which you can’t even see in the image above, probably each reduced my life expectancy by three years. They were a true pain in my Arsch to reach to the point where I actually wound up with a sore back for days due to me twisting myself into a pretzel.
Removing the hose and hose clamp from the shroud wasn’t a huge deal, but the forwardmost Allen bolt holding the pipe to the back of the shroud was awful, requiring me to snake my hand between the block and coolant pipe. My hands got banged up, my back was hurting from standing under this car on a hoist, I was tired, and I was cold.
All because I wanted to replace, as a precaution, a water pump that ended up being in perfectly fine shape.

Once I had the pump shroud off, I was able to get the pump and the accessory-drive bracket out of the engine bay and onto my workbench. I then lathered some silicon gasket-maker onto my new pump and shroud (I’d scratched the old shroud’s gasket surface during the extraction, so a new one seemed like a smart idea), and bolted the assembly to the back of the engine.
I then took the pulley off the old pump via vice grips, and installed the accessory bracket and pulley onto the new part using three new fasteners.

Things were looking up, until I tried installing my two serpentine belts. The first one required me to use a press to squeeze my tensioner. While in the compressed position on the press, I tightened some zipties around the tensioner to keep it in its smallest state so that I could bolt it up to my accessory drive.
This was extremely difficult, as that tensioner just makes so much tensile-force, and with my new belt being a bit shorter than the old one, even the fully-compressed tensioner seemed a bit too long. I had to force the tensioner into position using the leverage of a pry bar. It took me hours, and I may have cross-threaded a bolt. But it seems to hold, so I’m happy.

But the struggles didn’t stop there. The belt for my power steering pump seemed a bit short, too. No matter how much I loosened the tensioner (for this belt, there was just a basic mechanical tensioner bolt instead of a hydraulic tensioner), that belt wouldn’t slip under the new idler pulley (see above). To get the belt under the pulley, I tied four zipties around the belt, and hung my entire bodyweight off of them. The zipties snapped, but it was enough to get the belt mostly around the pulley. Turning the engine’s crankshaft pulley with a wrench a few times brought the belt fully into its proper position.
From there, I just buttoned everything up and adjusted the belt tension. It seems a bit tight, but not too bad.
This water pump and accessory belt job was far more difficult than it should have been, but this work—along with all the other work I’ve done on this van—is all the more reason to drive the wheels off this machine.
Anyway, I know I’m not the only one who has dealt with a tough wrenching dilemma. Talk me through a wrenching job that kicked your butt. Feel free to post pictures in the comments.
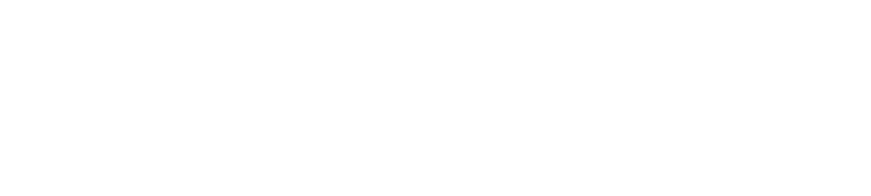