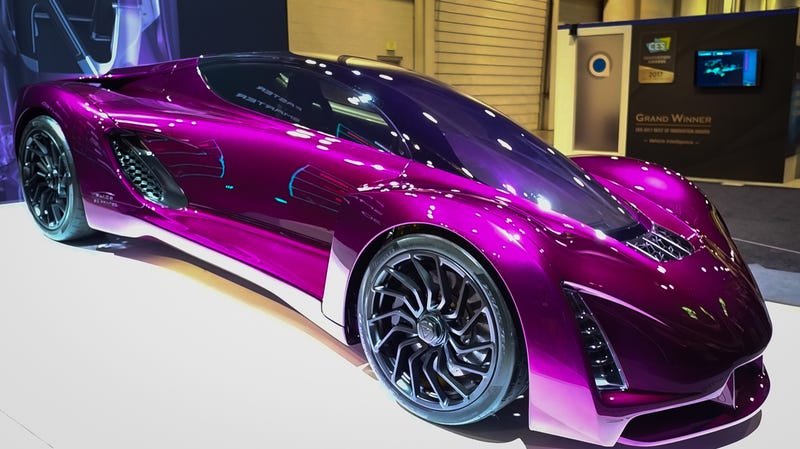
The hype around consumer 3D printers has mostly died down, but that hasn’t stopped the startup Divergent3D from barreling full steam ahead in the industrial printing world. The company debuted the first 3D-printed supercar—the Blade–two years ago and has since continued developing its printing methods. Now, it’s working with major industry players like Peugeot and SLM Solutions to use its printing methods at mass scale.
Advertisement
The reason why Divergent3D is so committed to industrial printing (despite the ridiculously high and costly risks) is that the benefits of printing car parts appears to be obvious: Printing components, rather than stamping them out using traditional injection molding or casting, lets carmakers customize every detail of a car part. It also lets engineers turn out ideas more quickly. Printing car components, at least in theory, will reduce the cost of retooling factory machines every time an engineer wants to try out a new idea. That will hopefully lead to more adventurous and more ambitious projects—exactly like The Blade.
One of the big benefits to Divergent3D’s printing methods is that it allows engineers to customize car components, essentially giving them even greater control over how a car is assembled. For example, they can add more material to specific stress points or leave holes in areas where it’s possible to reduce weight (something that makes the car way faster). The benefits can often be startling. That’s why The Blade’s chassis weighs only 1,400 pounds—about three times lighter than a Tesla Model S.
Advertisement
Because of these advantages, carmaker Peugeot has finally jumped on the 3D-printing bandwagon. The $12.8 billion partnership between Peugeot and Divergent3D is basically just the first step in a slow march for major carmakers that will more than likely take many years to be used widespread.
Still, it’s the first sign that a major carmaker is willing to give 3D printing parts a chance. The companies haven’t given any specifics about how many parts it will print and haven’t stated any specific goals for the partnership—but it’s clear that Peugeot is at least interested in exploring the cost savings.
Now for the drawbacks: You dont’s see more car companies 3D printing components for two big reasons. One is the rate of printing or basically the speed at which they can print car components. Right now, the process is way too slow—much like desktop printers—so it wouldn’t make sense for the biggest car companies to try to mass produce something like a Ford Taurus using a 3D printer.
Sponsored
The other major obstruction is the reliability of the materials. The printers used in industrial settings require lasers to melt metal powders, layer by layer, on top of each other until an object is complete. The problem is that it’s hard to guarantee that you’ll get quality materials every single time. This is obviously a huge risk for big carmakers and one that’s unjustifiable for now.
Of course, this will all change as long as companies like Divergent3D continue developing new partnerships and methods to increase reliability. Much like desktop printers, industrial-sized ones will also get faster. The materials will also become more reliable as companies begin to adopt these new methods.
Advertisement
Advertisement
It might be a long time from now, but if Divergent3D—and other companies like it—keep refining this technology, it’s hard to imagine why the biggest players in the car world wouldn’t want to adopt this production method in some capacity.
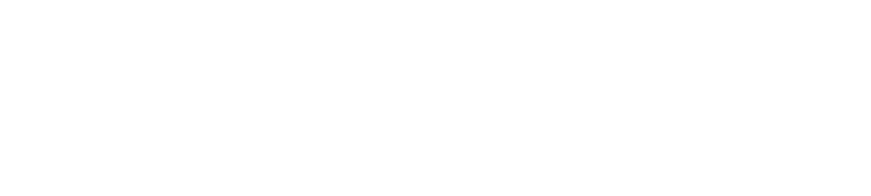